Meyers Personal Injury Law | January 24, 2024 | Product Liability
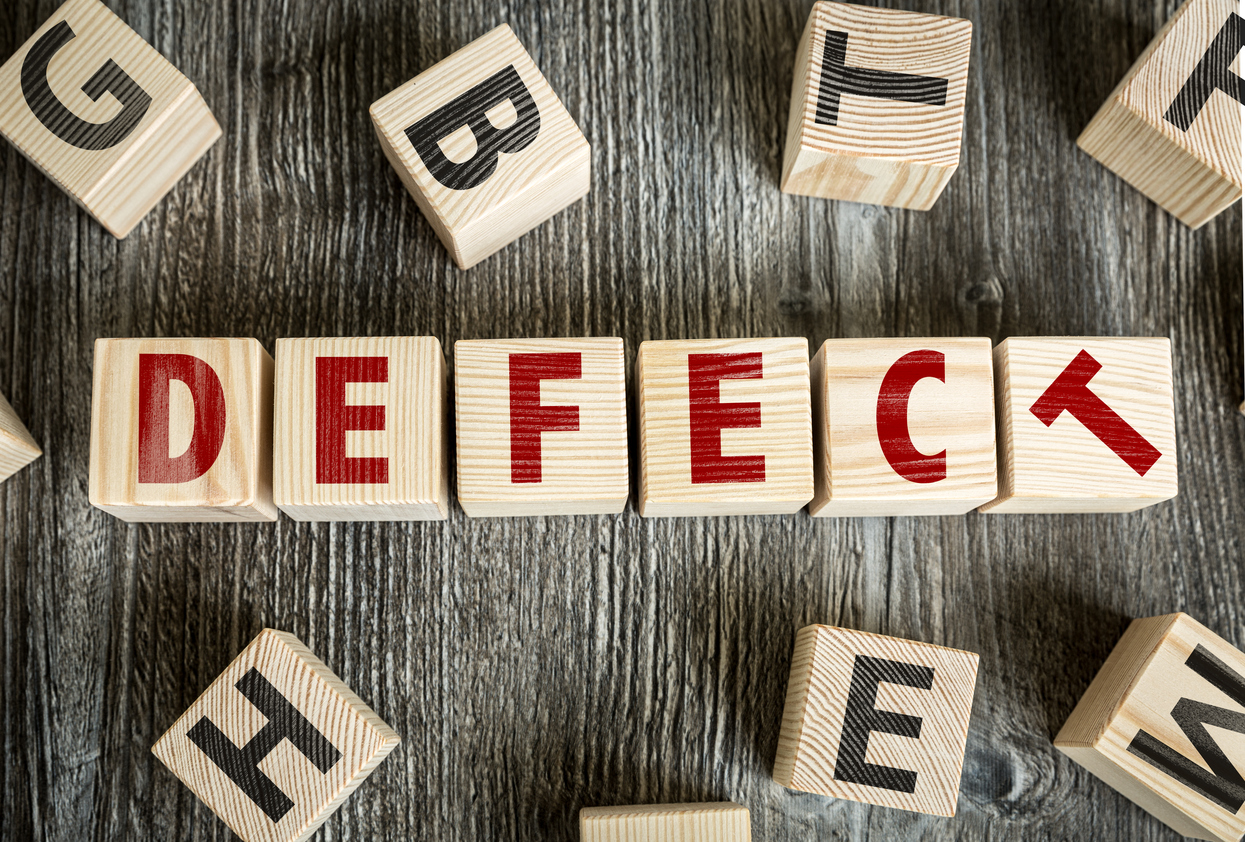
When consumers encounter a malfunctioning product, the defect can often be categorized as either a manufacturing defect or a design defect. These types of defects are fundamentally different in their nature and implications. A manufacturing defect occurs during the construction or production of the item, resulting in a product that deviates from the intended design or specifications. Such defects are typically unintentional and may affect only a subset of the produced items, often due to errors or issues in the manufacturing process at a factory or plant.
On the other hand, a design defect is inherent in the product’s blueprint and affects all units of the product line. This type of defect is rooted in the initial planning and development stages when the product’s design failed to ensure the safety and functionality of the end product. In cases of design defects, the entire product line may be flawed, posing potential risks or problems for users. Identifying the nature of the product defect is crucial for addressing liability issues, implementing recalls, and improving product safety standards.
Conceptual Overview
In product liability, it helps to distinguish between two different types of defects that can prompt recalls or legal action: manufacturing defects and design defects. These concepts form the basis for understanding potential flaws in the lifecycle of a product.
Definition of Manufacturing Defects
Manufacturing defects occur when there is a departure from a product’s intended design during its creation, despite the design itself being safe. These defects usually arise from errors in the assembly or production process. For example, a car might have a defective brake system not because the design is flawed, but because a component was improperly installed during assembly.
Definition of Design Defects
Design defects, in contrast, are inherent; they exist before the product is manufactured. This type of defect implies there is a fundamental flaw in the product’s blueprint, which makes the product unsafe even when perfectly assembled. For instance, a drug with a chemical composition that can cause harmful side effects would have a design defect.
Legal Framework
In product liability law, different legal standards apply depending on whether an issue stems from a manufacturing defect or a design defect.
Liability in Manufacturing Defects
Manufacturing defects occur during the construction or production of an item. Courts generally apply a strict liability standard, meaning that a manufacturer can be held liable for a manufacturing defect regardless of intent or negligence. Victims must prove that the defect caused harm while the product was used as intended.
Requirements for Liability | Manufacturing Defects |
---|---|
Proof of defect | Yes |
Proof of causation | Yes |
Product used as intended | Yes |
Manufacturer’s intent | No |
Liability in Design Defects
Design defects are inherent; they exist before the product is manufactured. Legal liability involves demonstrating that there was a foreseeable risk when the product was designed and that a safer, feasible alternative design existed. The risk-utility test and consumer expectations test are common legal standards used in such cases.
- Risk-Utility Test: Balances the product’s risks against its utility and cost.
- Consumer Expectations Test: Considers whether the product performs as safely as an ordinary consumer would expect when used as intended or in a reasonably foreseeable manner.
Standards for Liability | Design Defects |
---|---|
Foreseeable risk | Yes |
Safer alternative design | Yes |
Balance of risk and utility | Often |
Consumer expectations | Considered |
Identification
In the realm of product integrity, differentiating between manufacturing and design defects is crucial for quality control.
Detecting Manufacturing Defects
Manufacturing defects occur when products deviate from their intended design during production. Detection often involves:
- Quality Inspections: Regular checks at various production stages ensure each item matches the original blueprint.
- Testing: Subjecting a sample from a production batch to stress tests can uncover irregularities that aren’t visible to the naked eye.
Recognizing Design Defects
Design defects are inherent flaws due to a product’s conceptualization. Identification typically requires:
- Analysis of Consumer Feedback: Repeated safety concerns or malfunctions reported by users may indicate a potential design issue.
- Comparative Assessment: Examining how similar products perform can provide insight into whether a design is flawed.
Implications and Consequences
The differences between manufacturing and design defects carry significant implications and consequences, particularly regarding consumer safety and the legal accountability of companies.
Impact on Consumer Safety
Manufacturing defects often result in products that deviate from a company’s standards, potentially causing harm or malfunction. Design defects, however, suggest a fundamental flaw that can pose consistent risks to consumers across all products made to that specification. Both issues can lead to:
- Injuries or fatalities if the defect compromises critical safety features.
- Recalls that necessitate consumers to stop using the product until it’s fixed or replaced.
Legal Repercussions for Companies
Companies face different legal challenges based on the type of defect. Manufacturing defects can lead to:
- Lawsuits involving specific incidents linked directly to deviations in manufacturing processes.
- Fines imposed by regulatory agencies if the defect violates safety standards.
In contrast, design defects might result in:
- Class action lawsuits, as these defects generally affect all products with the same design.
- Larger-scale recalls and greater financial loss due to the systemic nature of the design issue.
Prevention and Mitigation Strategies in Tennessee
The strategies for preventing and mitigating manufacturing and design defects are critical in ensuring product safety and reliability. They require distinct approaches in quality assurance and risk assessment.
Quality Assurance in Manufacturing
In the manufacturing process, quality assurance is vital for preventing defects. The establishment of robust Quality Control (QC) procedures is essential. This involves:
- Regular Inspections: Each phase of production should be monitored with systematic checks to identify variances from quality standards.
- Testing Protocols: Finished products must undergo rigorous testing for performance and safety before they are released into the market.
Risk Assessment in Design
Risk assessment during the design phase focuses on eliminating defects before a product is manufactured. Key steps include:
- Design Review: Experts scrutinize the design to forecast potential failures, employing methods such as Failure Mode and Effects Analysis (FMEA).
- User Scenario Analysis: Designers must consider various user scenarios to predict misuse and accordingly adapt the design to mitigate inherent risks.
Case Studies
This section examines specific instances where manufacturing and design defects impacted products and consumers.
Historical Manufacturing Defects
The Ford Pinto case serves as a classic example of a manufacturing defect. This issue revolved around a faulty fuel tank design, but it was the improper assembly process that led to the notorious fires upon rear impact. Ford faced multiple lawsuits due to this defect.
Tylenol faced a crisis in 1982 when cyanide-laced capsules resulted in seven deaths. The problem was traced back to tampering after the products left the manufacturing plant, highlighting a severe manufacturing control defect related to packaging security.
Significant Design Defects Cases
In the world of electronics, Samsung Galaxy Note 7 represents a significant case of design defect. Devices began to catch fire due to a design flaw in the battery compartment that led to overheating. Samsung had to recall millions of units and discontinue the product line.
The Dalkon Shield IUDs were implanted in numerous women in the 1970s and led to severe health complications. The design defect involved a multifilament string that acted as a conduit for bacteria into the uterus, resulting in infections and, in some cases, death.
Future Trends
The trends in manufacturing and design are intricately linked to advancements in technology and methodologies. These developments have significant implications on defect reduction in both areas.
Advancements in Manufacturing Technologies
Automation and Robotics: The integration of advanced robotics and automation in manufacturing processes is leading to more precise and consistent production. This reduces the occurrence of manufacturing defects as robots can maintain standards with a high degree of accuracy.
- 3D Printing: Additive manufacturing technologies, particularly 3D printing, are allowing for complex designs to be produced with fewer defects. Materials used in 3D printing can be tested and customized for optimal performance, minimizing the chances of defects stemming from material limitations.
Evolving Design Methodologies
Computer-Aided Design (CAD): Enhanced CAD software now offers more sophisticated simulation tools. Designers can detect potential design defects early in the development process. This results in products that are less likely to suffer from design defects.
- Sustainable Design Principles: There is a shift towards sustainable design that balances product functionality with environmental impact. This approach often involves using new materials and innovative designs that reduce the product’s ecological footprint while also minimizing the risk of design defects.
Contact Our Nashville Personal Injury Law Firm Today at Meyers Personal Injury Law
If you were injured in an accident in Nashville or Brentwood and need legal help, contact our Nashville personal injury lawyers at Meyers Personal Injury Law to schedule a free case review today.
Meyers Personal Injury Law Nashville
1308 Rosa L Parks Blvd Suite 101,
Nashville, TN 37208
(615) 258-9000
Meyers Personal Injury Law Brentwood
105 Continental Pl Suite 100,
Brentwood, TN 37027
(615) 258-9000